The fusion of simulation tools with AI and machine learning is transforming automotive electronics. Mukul Yudhveer Singh of EFY discusses this technological shift with Shitalkumar Joshi, Senior Director Application Engineering, focusing on its impact on vehicle design.
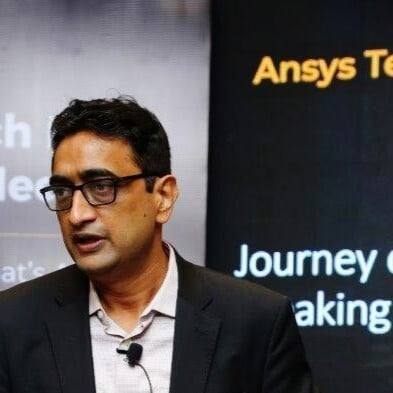
Q. How are simulation tools enhancing the reliability and safety of automotive electronics?
A. The automotive industry has long been a pioneer in the use of simulations, but the increasing complexity of critical electronics now demands even more advanced methods to ensure both safety and reliability.
Automotive electronics must endure extreme conditions—such as vibrations and fluctuating temperatures—over a span of 10-15 years. These systems are safety-critical, especially for functions like autonomous driving, crash detection, and electronic power steering. To address these challenges, the industry is turning to reliability techniques such as physics of failure analysis, which identifies potential problems in extreme conditions.
With the rising number of electronic components in vehicles, the risk of electromagnetic interference (EMI) has grown significantly. This interference can degrade performance, cause unintended malfunctions, or even lead to the failure of safety-critical features. Engineers now rely on simulation to meet electromagnetic compatibility (EMC) standards, ensuring the product’s robustness in real-world conditions.
Crash safety is another key focus, driven by initiatives such as the New Car Assessment Programme (NCAP). Companies extensively use simulations to achieve high safety ratings while reducing reliance on physical tests. Simulations now incorporate detailed human body models to enhance both child and passenger safety, leveraging computational power for more accurate crash modelling.
Ultimately, simulations operate across various scales and disciplines to ensure the electronic and structural reliability of individual components as well as entire vehicles.
Q. How do physics-based simulations boost efficiency in EV and autonomous vehicle development?
A. For electric vehicles (EVs) and autonomous systems, physics-based simulations are no longer a luxury—they are essential. Modern vehicles are intricate cyber-physical systems, and this complexity demands a quicker time-to-market. There are three primary areas that significantly benefit from these simulations: sensors, high-voltage electronics, and embedded software/hardware.
Sensor design incorporates principles from optical, electromagnetic, and thermal physics. High-voltage electronics, such as those found in EV powertrains—including motors, batteries, and power electronics—require thorough electro-thermal analysis and structural reliability testing. As for embedded software and hardware, simulations assess the reliability of printed circuit boards (PCBs) and chips through physics of failure approaches, alongside model-based software development testing (MBSE).
By integrating these advanced simulation techniques, the automotive industry is able to design components from the ground up, merging them into cohesive virtual systems that enhance development efficiency across the board.
Q. How do physics-based simulations enhance the safety and efficiency of EV motors, controllers, and batteries for unmanned conditions?
A. Physics-based simulations allow system-aware component design and informed material selection tailored to specific conditions. Motors must be designed with the specific vehicle and environment in mind, as a one-size-fits-all approach is ineffective. For instance, motors require detailed electromagnetic and thermal analysis in India’s diverse climate. High temperatures can cause them to lose magnetic properties, leading to increased losses and power consumption, which reduces the vehicle’s range. Simulations help predict power consumption under various conditions and driver behaviours, enabling designers to tune motor controllers for specific needs, such as high-speed sports mode or extended range.
Secondly, material selection is critical for efficiency and safety. Designers must consider cost-effectiveness, supply chain availability, and sustainability when choosing materials. Tools like the Ansys Granta Materials Intelligence™ platform assist engineers in making informed decisions on material selection and substitution, ensuring performance and sustainability even if a supplier becomes unavailable.
For batteries, designers must account for factors such as available space, weight, and cooling capacity, especially when considering different vehicle types like two-wheelers, three-wheelers, four-wheelers, or SUVs. By considering these environmental parameters, simulations enable the creation of battery cells, modules, and packs that meet specific range predictability and safety requirements.
Q. How is AI/ML transforming traditional deterministic simulations in engineering applications?
A. Traditionally, simulations are deterministic, relying on set equations. However, artificial intelligence and machine learning (AI/ML) are transforming this process despite the limited data available in engineering product design. The emerging trend is physics-driven neural networks, which can work with minimal data to provide higher accuracy models. This hybrid approach of AI-ML and physics-based simulation provides much higher benefit to design and validation engineers than any of these two methods can provide individually
Q. Does Ansys offer any solutions which incorporate AI/ML?
A. Ansys has a multifaceted approach to using AI. The newest AI solution from Ansys, called SimAI, is a physics-agnostic application that combines the predictive accuracy of Ansys simulation with the speed of generative AI. The state-of-the-art technology uses the shape of a design itself as the input, facilitating broader design exploration even if the shape structure is inconsistent across the training data. The application can boost the prediction of model performance across all design phases by 10-100X for computation-heavy projects.
The second set of AI offerings are clubbed as Ansys AI+ technologies. Ansys AI+ enables customers to augment simulation with add-ons, offering more options and variety in accessing artificial intelligence capabilities across Ansys desktop products. Select Ansys AI+ technologies, including the Ansys Granta MI AI+ module, for more significant insights into material-process-property relationships. Ansys optiSLang AI+ module for sensitivity analysis, optimisation, and robust design. Ansys CFD AI+ module for turbulence modelling.
And finally, Ansys GPT expands Ansys artificial intelligence integration across its simulation portfolio and customer community, AnsysGPT. It is a multilingual, conversational, AI virtual assistant set to revolutionise how Ansys customers access the knowledge base. Developed using advanced ChatGPT technology available via the Microsoft Azure OpenAI Service, AnsysGPT uses well-sourced Ansys public data to answer technical questions concerning its products, relevant physics, and engineering topics within one comprehensive tool. So, you see,AI-based AnsysGPT is adding great value to the Ansys customer experience.
Q. What are the new trends or upcoming add-ons in simulation that automotive electronics should look forward to?
A. We have recently observed significant trends in integrating AI and ML with physics-based simulations. Historically, AI and simulations were seen as separate domains; AI was primarily for data analysis, while simulations were based on first-principles physics. However, recent research has shown that AI can significantly enhance simulations. AI integration allows for an exponential increase in the number of designs that can be studied using simulations, thus expanding the design space engineers can explore.
Another trend we see is the shift towards high-performance computing (HPC). Traditionally, simulations have been CPU-intensive, often requiring hours or days to complete. Our customers are now adopting graphic processing unit (GPU) and cloud-based solvers. Cloud computing is becoming more prevalent in simulations. Although there was initial resistance due to concerns about the security of design and intellectual property data, the scenario is changing with time. Sensitive data in finance and other sectors are already on the cloud, and simulation solvers are now following suit.
The third trend involves a digital transformation in product development processes, which handles the complexity of modern cyber-physical systems by integrating various components, subsystems, and system models in a virtual environment.
Q. How are OEMs and suppliers enhancing virtual vehicle testing through model interoperability?
A. OEMs and suppliers are now shifting their focus on sharing behavioural models on top of sharing physical prototypes. Traditionally focused on hardware, many tier-1 suppliers are now venturing into electronics, with some even supplying entire powertrains. OEMs either source these powertrains from tier-1 suppliers or develop them through complete vertical integration. To prepare final vehicles for the road, OEMs must analyse the entire system in a virtual environment. This requires access to models and behaviours of all components, whether developed in-house or by suppliers. Suppliers now use simulations to design components and provide these specifications to OEMs, along with behavioural models. This exchange allows them to perform comprehensive vehicle-level analysis in virtual settings, facilitating thorough testing and validation. This collaborative approach between OEMs and suppliers improves the efficiency and accuracy of virtual vehicle testing.
Q. Does simulation play a role for tier-2 and tier-3 suppliers in addition to automotive OEMs and tier-1 suppliers??
A. Across the entire supply chain, simulations are being used for different domains and applications. For mechanical components, it is essential for optimising material use and achieving cost-effective, lightweight designs across the supply chain. Simulations are conducted for both individual components and larger systems to evaluate the overall performance of any physical product integrated and test it for durability, performance, and safety within the automotive distribution network .
For electronics components, multi-domain simulations and software practices are deployed. Tier-2 suppliers, such as TI and Renesas, are integrating electronic simulations into larger products by providing software controls for the automotive industry. This shift involves vehicle-aware chip design, where simulations are essential. A model-based embedded software development and simulation environment with built-in certified automatic code generation functions are increasingly used for safety critical applications like BMS and ADAS. EMC is ensured by use of simulations prior to certification tests.
Q. Can tier-1, tier-2, and tier-3 suppliers jointly simulate a complete solution before physical assembly?
A. Yes, all tier suppliers can jointly simulate a complete solution before physical assembly by forming consortiums to enable collaboration while protecting intellectual property. Each supplier conducts their own simulations to safeguard their IP. But, for comprehensive simulations, OEMs need access to the component’s behaviour models, requiring interoperable data models across organisations. This allows for exchanging simulation models instead of physical prototypes, enabling pre-prototype integration and analysis.
While some models are easily interoperable, software controls pose more challenges. Integrating software from different suppliers with hardware is vital. An integrated approach, where software from various suppliers interacts with the hardware, is highly desirable and can significantly reduce car development times from 6 years to 2-3 years. This method, known as virtual vertical integration, allows for simultaneous model development and integration testing. Although not all OEMs produce components in-house, they benefit from integrating designs, data, or models from their suppliers to virtually create a fully integrated vehicle . This approach is increasingly pursued, especially in Europe, to streamline development processes.
Q. What is the simplest way for companies to experience and understand simulation benefits without significant investment in software and personnel?
A. We collaborate with industry partners and government bodies to address the challenges that hinder the adoption of simulation practices and increase awareness. We have established a center of excellence (CoE) with the Automotive Research Association of India (ARAI) in Pune, focusing on innovations in EV energy storage and ADAS. We are also partnering with companies like TCS and Spark Minda to set up CoEs for electrification, connectivity, electronic safety, and security. We work with premier research institutes, including IITs and key colleges, to develop curricula tailored to automotive and advanced skills such as motor and battery physics-based simulations, to democratise access to simulations, improve ease of use, and increase the availability of experts and resources. By fostering industry and academic partnerships and demonstrating a clear ROI, we strive to make simulation tools more accessible and beneficial for all players in the automotive sector.
Q. Besides automotive and aviation, which other industries are adopting these technologies?
A. Our most significant segment is high-tech electronics, expected to be as large as, if not larger, the automotive and aerospace sectors. In electronics, the same principles apply across various branches of physics—structural, fluid dynamics, thermal dynamics, and electromagnetics. These principles are used in motors, transformers, antennas, radars, 5G phones, PCBs, and optical devices such as cameras. The same physical principles are applied to electronics in the automotive and aerospace industries. For instance, automotive electronics must last for around 15 years, enduring extreme temperatures and vibrations, while consumer electronics like smartphones are expected to last three to four years. Despite their shorter lifespan, smartphones face challenges due to their compact form factor, increasing power and processing capabilities, and thermal issues. Smartphones incorporate multiple antennas (Bluetooth, and GPS) that must function without signal interference, ensuring quality reception from various angles. Thus, extensive electromagnetic analysis is performed on smartphones and other electronics to optimise performance.
Healthcare is an emerging industry for us where the industry is adopting what is known as ‘an in-silico’ approach, where engineering simulations are used throughout the development, validation and also regulatory processes. The virtual practices foster the innovations and reduce cost and time of introducing new products.
In the energy industry, simulations are enabling a safe, fast and reliable transition to a new low-carbon energy mix to meet energy needs in a sustainable manner. Green hydrogen, wind mills, oil-n-gas optimisation, new age nuclear reactors – are benefiting by simulations.
The simulation also supports Industry 4.0 by transforming simulation and sensor data into actionable insights. Other industries include Material and Chemical processing, industry uses simulation to model processes aiming at reducing operational cost in the plants.
Finally, space is the most daunting and unforgiving environment where physical tests are limited. Ansys offers simulation solutions that address all the needs of space missions—designing launch systems and spacecraft, planning operations, and sustaining missions. More importantly, our solutions can be combined to achieve an enterprise-level digital engineering environment that integrates with other software tools and data.
So apparently, simulations are pervasive across all industries. From sustainable transportation and advanced semiconductors to satellite systems and life-saving medical devices, the next great leaps in human advancement are powered by physics-based simulations.